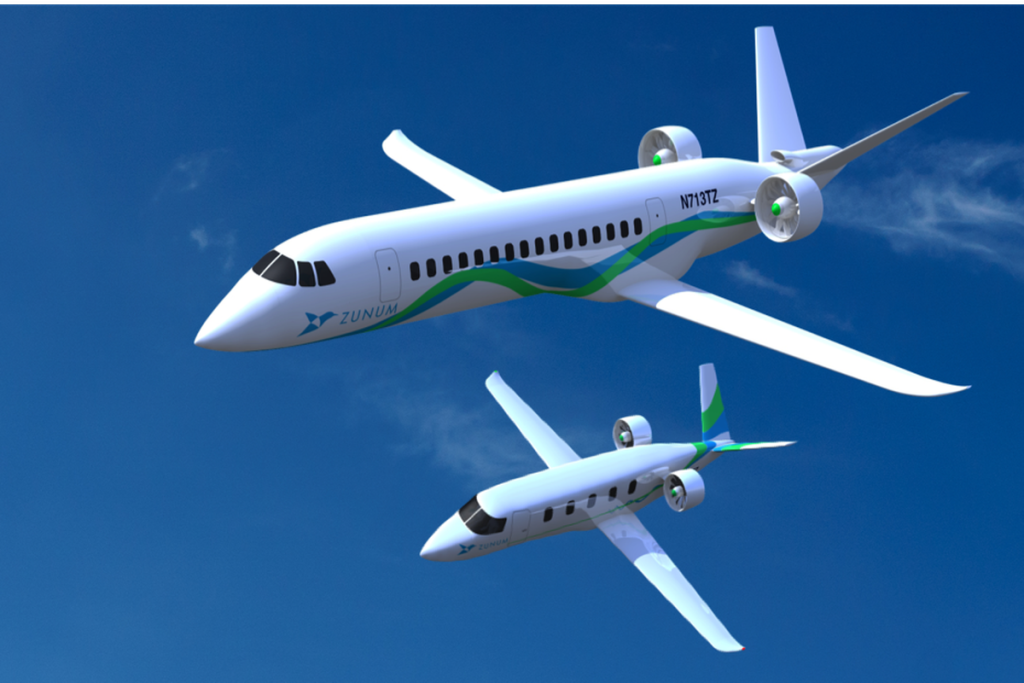
Can We Replace Large Commercial Aircraft with Fully Electric Equivalents?
The aviation industry faces mounting pressure to reduce carbon emissions, which accounts for about 3% of worldwide greenhouse-gas emissions. The idea of electric aircraft has captured the imagination of engineers and environmentalists alike. While small electric planes have already taken to the skies, the prospect of replacing large commercial aircraft with fully electric equivalents presents a formidable challenge. This article explores what it would take to make this vision a reality.
Current State of Electric Aviation
Electric aviation is still in its infancy. Current electric aircraft are primarily small, short-range planes designed for personal use or pilot training. These planes are limited by their range, speed, and payload capacity. In contrast, large commercial jets, like the Boeing 747 or Airbus A380, carry hundreds of passengers over thousands of miles. The gap between the capabilities of today’s electric aircraft and the demands of large commercial jets is still huge.
5 Big Hurdles to Overcome:
1. Battery Technology and Energy Density
The biggest hurdle in electrifying large commercial aircraft is battery technology. Jet fuel is extremely energy-dense, packing a significant amount of power into a small volume. Current lithium-ion batteries, while suitable for small electric planes, are far less efficient in terms of energy density. To match the performance of jet fuel, an electric aircraft would require batteries that are prohibitively large and heavy, significantly affecting the aircraft’s design and performance.
The data we’ve provided below puts into perspective the significant energy requirements for two types of aircraft engines, along with the corresponding number of lithium-ion battery cells needed to match their power outputs.
Note that these are calculations based on ideal cases and may not reflect the real situation.
Here’s a breakdown of how these calculations and comparisons might look:
Power Output of Different Aircraft Engines at Full Throttle
Commercial Jet Engines (e.g., GE90-115B)
The GE90 engine, with an approximate power output of 512 kW (converted from 115,000 pounds of thrust), would require around 71,111 lithium-ion battery cells to match this power in an idea situation
Piston Engines (e.g., Lycoming IO-360)
With a power output of 149 kW, approximately 20,694 lithium-ion battery cells would be required to sustain this level of power in an ideal situation.
Note:
Energy Conversion: The power outputs of these engines are converted into electrical power (kilowatts) using standard conversion factors, which helps compare the traditional fuel-based power systems with an electric equivalent.
Battery Requirements: Each lithium-ion battery cell is assumed to have an energy capacity of approximately 7.2 Wh (3.6V * 2Ah). Based on this capacity, the number of cells needed to generate the required power is calculated. This will sustain the operation for approximately two hours.
Implications for Electric Aviation
The sheer number of battery cells required to match the power output of traditional aircraft engines shows the challenge of electrifying large aircraft. For example:
Weight and Space: The weight and volume of the batteries needed for a commercial jet engine could be immense, posing significant challenges in terms of aircraft design and performance. It is also important to note that the weight of these batteries does note change throughout the flight affecting MTOW (Maximum Take-off Weight) and MLW (Maximum Landing Weight).
Efficiency: The efficiency of electric propulsion would depend not just on the energy density of the batteries but also on advances in battery technology that can provide higher capacities with lower weights.
Feasibility: While smaller aircraft might be more feasible to electrify with current technology, large commercial jets would require substantial technological advancements before electric power becomes a viable alternative.
Advancements in battery technology, such as solid-state batteries or alternative energy storage methods like hydrogen fuel cells, offer some hope. However, these technologies are still in the experimental stage and are years, if not decades, away from being viable for large commercial aircraft.
2. Aircraft Design Considerations
Replacing jet engines with electric propulsion systems would require significant changes in aircraft design. Electric propulsion systems might necessitate larger wings to accommodate additional batteries and provide the necessary lift. Lightweight materials would become even more critical to offset the weight of the batteries. Additionally, new designs like distributed propulsion systems or blended wing bodies and hybrid electric aircraft could help improve efficiency, but these innovations are still in the conceptual phase and would require extensive testing and validation.
3. Infrastructure and Charging Requirements
Another major challenge is the infrastructure needed to support electric aircraft. Airports would need to be equipped with high-capacity charging stations capable of delivering massive amounts of electricity in a short time. The current fuel supply infrastructure, with its well-established refueling processes, would have to be entirely rethought. Battery swapping could be a potential solution, but it would require standardization across the industry and additional logistics to manage battery storage and transportation.
4. Economic and Environmental Impacts
Transitioning to fully electric large commercial aircraft would be expensive. The development costs, combined with the need to redesign aircraft and build new infrastructure, could drive up the price of air travel. However, the long-term environmental benefits could outweigh the initial costs. Electric aircraft could drastically reduce the aviation industry’s carbon footprint, though the environmental impact of producing and disposing of large quantities of batteries must also be considered.
5. Regulatory and Certification Challenges
Even if the technical challenges are overcome, regulatory hurdles remain. Certifying new technologies for use in commercial aviation is a rigorous and time-consuming process. Safety standards would need to be established, and new testing protocols would need to be developed. International aviation authorities would play a critical role in setting these standards and ensuring that electric aircraft meet the same safety and reliability criteria as their fossil-fuel-powered counterparts.
With this in mind,
The process of replacing large commercial aircraft with fully electric equivalents is a daunting task that involves overcoming significant technical, economic, and regulatory challenges. While the vision of fully electric aviation is appealing, it remains a distant goal. Continued research, innovation, and collaboration across the industry will be essential to making this dream a reality. Until then, incremental improvements, such as hybrid-electric systems, may serve as a bridge to a more sustainable future in aviation.
What’s your take on this?
The Aviator Newsletter is dedicated to sharing educational stories rooted in real-world experiences and providing updates on the latest developments in aviation engineering. It offers industry insights, expert opinions, and practical advice, making it an essential resource for aviation professionals and enthusiasts alike. Whether you are an engineer, a pilot, or simply passionate about aviation, The Aviator Newsletter keeps you informed and inspired.